Dry mixes: types and features
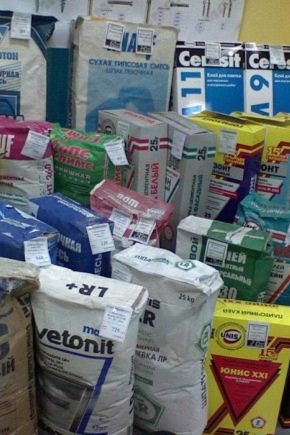
Building solutions for many centuries were prepared directly on the sites where they worked with them. But this creates a number of inconveniences and problems, since it is very difficult to maintain exact proportions and to observe the mixing technology.
After all, conditions at a real construction site are rather far from standard, no matter how hard everyone tries to maintain cleanliness and order.
Special features
Some home craftsmen and even amateur builders are wondering why dry mixes are needed at all if you can make the usual solution yourself.
Compared with home-made solutions, a dry mix of industrial manufacturing has several important advantages:
there is no need to self-dose all components and spend time on it;
proportions are initially correct and comply with regulations;
can be limited to the addition of water and thorough mixing.
But even these three circumstances do not exhaust the merits of a dry mix. Often there is a situation when tens and even hundreds of kilograms of mortar are required to fill the floor screed. It is quite easy to buy cement, lime, and so on, but it is extremely difficult to buy the necessary amount of high-quality sand. In most cases, the procurers sell it in large batches, and independent mining is economically unprofitable. For repairs in an apartment or other room on the second and subsequent floors, the traditional cement and sand screed is quite heavy. If you prepare a solution of dry mixes, you can reduce the load on the overlap.
It will be possible to put on top a heavier finishing material or reduce the requirements for the strength of the foundation. Yes, and reducing the weights that will have to be lifted to the floor and transported around the house will only be a plus.There is no special need to use concrete mixers and mixers, you can prepare a solution from an anhydrous combination for casting floors in a large plastic container using nozzles on electric drills. At the same time, 0.5 cm of dry screed for hardness and portable power loading is identical to 3 cm of the classic version of cement and sand. Special additives reduce the drying time of the coating and ensure self-leveling of the screeds without the need to work on them additionally. Manufacturers have established the production of mixtures, adapted for dry and wet rooms, for roughing and finishing.
Types and specifications
Despite the wide range of dry solutions currently available, they all fall into one of two basic categories - the cement or plaster group. The first group is based on cement of the fine fraction, but this does not mean that it is also homogeneous. So, when the mixture is prepared for a subfloor, expanded clay or granite crumb is used as a filler. Such substances help make the floor 3-4 cm thicker.
But the draft composition is not suitable for laying most facial materials, and therefore on top of them make more layers of finishing mixtures.
For the preparation of the final parts of the screed used a combination of fine cement with carefully selected plasticizers. The main purpose of using such mixtures is the formation of a very smooth and extremely smooth base, on which it will be easy to lay even a laminate or linoleum. With a carefully selected recipe and strict adherence to technology in production for the final alignment just enough layer of 1 cm.
In order to obtain a self-leveling compound, extremely fine fractions of fillers are used - particles have a maximum diameter of 0.03 cm. And even this is not enough, you will need to use special components that will make the coupler level. When performing repair work, they often make a coupler for a warm floor, this task has special requirements for the material.
It should be:
plastic;
good heat transfer;
withstand a solid load.
Gypsum mix, unlike concrete, dries quickly and costs less. At the same time, the level of thermal insulation and noise containment completely meets the requirements of consumers. For the preparation of gypsum mortar take filling substances with a small diameter andvarious threads of mineral origin, which significantly increase the strength of the structure. The problem can be only in one: the mixture on the basis of gypsum can not be considered waterproof. It is absolutely unacceptable to use in rooms where the humidity level is above average.
A dry screed is placed on both wood and concrete. The need for carrying out wet works disappears and it is not even necessary to wait until the floor is ready for operation. For comparison: a typical sand screed or a wet mixture will dry for 25 days, combinations on the basis of gypsum will dry within 15 days. Before the end of this time it is unacceptable to mount the front cover, it will simply block the flow of water out and lead to unpleasant consequences.
The mortar mixture intended for outdoor use must necessarily contain substances that increase resistance to cold. In the presence of their coating will not only calmly endure the harsh winter, but can be applied even in the cold season. In the majority of mixes this or that saline solution is applied for this purpose.
As for the general classification, builders and sellers distinguish the following types of dry mix by typepossible works:
putty;
plastering;
floor standing;
protective (stopping the negative effect of the weather);
assembly;
masonry;
decorative;
primer;
waterproofing.
In addition to cement and gypsum, a number of polymers, lime, and even more complex combinations can be used as a binder. Their diversity allows us to provide such ambiguous and even contradictory properties.
Dry mixes for waterproofing help build underground and subsurface structures, preventing the negative effect of moisture on their basic materials. The penetrating variety of this material contains cement base, aggregate and various kinds of additives. The porous structure of the material allows additives to very easily contact with the main components throughout the coating. The result is a durable and hydrophobic layer.
Capillary dry mix is needed for waterproofing horizontal surfaces. The period of its service is practically unlimited; it is comparable with the time of operation of the wall itself. Injection formulations help to eliminate the defects that have already appeared.Mix M200 is designed to create masonry and allows you to repair concrete walls, handle the seams of building blocks. It can also be used for laying paving slabs for the preparation of plaster. The chemical basis of the material is portland cement and washed river sand.
The mixture on a lime-cement base in its practical characteristics far exceeds the gypsum analogue, it is resistant to infection by fungi and cracks a little, it is well applied to wood. Builders appreciate this material because of its plasticity and long drying time.
Cement mixture for the initial leveling is filled with expanded clay gravel, coarse sand or granite chips. Such combinations allow you to create a tightening layer over the heating equipment, but the expanded clay mixture is an exception to this rule. To lay the linoleum or carpet, you will need to put the finishing layer on top, the tile can be placed directly on the rough mass. In the courtyards and on landings, such screeds can be self-covering.
Consumption
Solution consumption per 1 m3 depends on which proportions are ideal for a particular type of mixture. In this case, whether the composition is used to fill the floor screed or to create a full-fledged concrete block is not important. Important: the amount of cement also does not matter, it will not affect the volume. Cement particles are extremely small and enter the gaps separating one grain of sand from another.
To obtain a mortar category M200 using a binder grade M500, you need to enter 25% cement and 75% sand. 1 cu. m of sand has a mass of 1.4 tons, which means the amount of cement will be 350 kg. The total weight reaches 1.75 tons.
But this is an average figure and, moreover, excluding the addition of water.
The severity of the mixture is determined by the proportion between sand and cement., as well as the fraction of the filler (the larger its particles, the heavier the mortar). Of course, the thicker the layer that is created, the more bags of building materials you will need to use. The calculation is relatively simple, when the mass is known, you only need to divide it by 50 kg (the standard value of the capacity of the bag). Consumption of dry mixes for sealing joints is determined in accordance with the manufacturers instructions, each composition is strictly individual in its characteristics.
Manufacturers
Factories for the production of building materials have responded to the demand from professionals and amateur builders predictably and brought to the market many options for dry mixes. But in order to avoid problems, it is necessary to buy only high-quality formulations produced by leading manufacturers.
Mark Knauf different impeccable reputation. The product range of the German concern includes products from gypsum and cement, some of the options contain expanded polystyrene granules. With the help of German mixtures, it is possible to fill in extremely thin bases, whose thickness ranges from 0.2 to 1.5 cm.
Another famous brand is CeresitIt is also famous all over the world and is presented in a variety of options.
The leading Russian manufacturer is "Founds"which makes at once two types of mixes for draft work. One of these types is needed to prepare underfloor heating, and the other can be the basis for a thin floor.
Mixtures Volma externally diverse, but all of them are intended for interior work in bathrooms and for cladding facades.
Varying the composition of the mixture, technologists can give it some qualities that allow:
to finish the building inside or outside;
prepare the surface for finishing;
strengthen the walls;
provide a normal microclimate in the house.
All brand products Volma made on the basis of gypsum and dry for 7 days. Thanks to specially selected additives, they are very durable and adhere to the surface thoroughly.
The color is usually white, light gray or gray.
Products of the company "Hercules" produced in Siberia and fully takes into account all the details of the Russian climate. It will help to build a screed, repair and wipe all sorts of seams, to eliminate deformations and potholes. In the production process, modern dosing equipment, carefully selected materials and techniques developed over the years are used. The company has established the production of plasters, plaster and polymer based putties, masonry and tightening cement compositions, alabaster, waterproofing and repair mixtures. Any of these materials perfectly tolerates the action of water, mechanical stress and is quite elastic.
Under the brand "Stone Flower" Mounting and masonry mixes of dry type mark M200 are produced. This composition is formed of Portland cement and dry sand.
The purpose of its application:
brick laying;
sealing of seams and elimination of problems with them;
concrete pouring stairs;
floor repair.
Used mixture easily tolerates cold, exposure to water, and other adverse factors. The developers were able to achieve high efficiency and ductility. The optimum temperature range during operation is from +5 to +30 degrees. Excellent adhesion is provided to cement-lime, cement-sand bases, concrete and bricks of all types.
Application and method of painting
To prepare a dry mortar and bring it into operation, you need strictly for the very recipe, which is developed by the manufacturer. To work will require water heated to 70-80 degrees, the amount of fluid must be determined individually. For mixing required to use a cyclical or continuous apparatus. It is necessary to clearly separate the solutions in light and heavy groups. The film composition is designed to protect the main structure from the effects of water on the surface, penetrating works in the whole volume.
Manual mixing of dry mix is quite possible, but a special mixer is much more appropriate., it saves both time and effort.That is why professional builders always use just such equipment, which allows them to perform work promptly. At home, you should buy an electric drill with a stirrer (a special nozzle in the form of a whisk). The tool must be taken after checking that it is perfectly clean.
When working, pour water and only then pour dry mixture into the container.
After waiting for the settling of dust, they begin to mix the composition at medium speed. It is very important to hold the drill or mixer firmly so that the tool does not break out of hand. In the process of mixing, it is allowed to add both water and new portions of the mixture, which allows varying its density and plastic properties.
Aqueous emulsion inks are usually applied to dry mixtures using long-hair rollers. To handle the corners and joints, you need to apply paint brushes. You can adjust the painting with a narrow brush. Work on painting starts from the corner, and on the ceiling from the joint with the wall, which falls on the corner farthest from the entrance.
Any water-based paint is applied in three layers:
parallel to the light from the window;
at right angles to it;
towards the window.
Tips
Dry construction products are often used for the floor, because it is one of the easiest ways to align and strengthen the structure. Cement-based mixtures perform best, and gypsum is somewhat worse. Only for solving a narrow range of tasks it is advisable to use quartz sand of fine fraction and limestone. To create a rough tie on a highly uneven ground, large fractions are needed. If the relief defects are relatively small, it is advisable to use a mixture with particles up to 0.5 mm.
Wooden floor is advisable to align the mixture with the inclusion of synthetic fiberglass. Before buying, it is advisable to find out the exact date of production, since even the best paper packaging with a plastic layer inside can not protect against the contents getting wet. It is advisable not to buy funds made over 3 months ago, they are almost guaranteed to be worse than the ones shipped recently. Cement leveling machines are recommended for heavily deformed surfaces and for making roughing layers.
Gypsum is unacceptable for work in areas where there is a high concentration of water, as well as where the surface of the floor is experiencing significant stress. Professional hand tools are required to fill large areas of the floor. Finishing in such areas is done in sections, which are separated by seams no higher than 1 cm. At least two people need to start working, because the ready-made solutions dry quickly.
Before laying the rough layer, the base must be cleaned from dust and dirt.
The room should be free from furniture and foreign objects. After cleaning the base with a construction vacuum cleaner, it must be primed. When the substrate intensively absorbs the primer primer, two overlapping layers are required. It is strictly unacceptable to introduce an excess amount of water and add to the dry mixture of foreign substances that are not provided for in the manufacturer's instructions.
Leveling compounds should be applied at a humidity of not more than 85-90% at a temperature of +5 to + 25 degrees. You should never eat more dry mixes per 1 square. m floor than specified by the manufacturer.A gross error will also be the use of finishing material for finishing and correcting defects of the rough base. When the coating is dry, unwanted voids may appear in the cement layer.
To simplify the alignment of the walls in the house or apartment help plaster beacons, which are made of galvanized rail and fasten strictly according to the indications of the construction level. To level the mixture deposited on the wall, the rule of metal is required.
There is another trick: they stick a reinforcing mesh made of plastic on the walls, this will also facilitate the formation of a layer.
To choose the right dry mix, you need to take into account three main circumstances:
terms of work performance;
degree of curvature and surface relief;
the cost of a particular product (which is also affected by the brand).
The higher the cement grade number, the stronger the mixture will be. But it is possible to cover the walls in a house or apartment with relatively weak cements of category M150. On a concrete surface that is not covered with a reinforcing mesh, you can apply a maximum of 2 cm of the mixture, and if the wall is made of brick, this figure is a maximum of 2.5 cm.
Careful selection of dry mix is extremely important for the solution of the tasks.If you follow all the rules for its application and preparation, you can guarantee the elimination of critical moments. But in case of the slightest doubt and in the absence of confidence in their abilities, it is more correct to turn to specialists.
How to distinguish the original dry mix from a fake, see the following video.