Fiber cement panels for exterior home
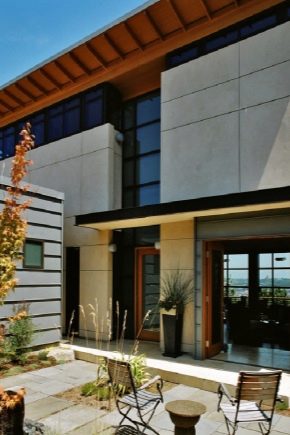
Today's construction market offers many options for facade materials. One of them is fiber cement panels, allowing to give the building a respectable appearance. In addition to its attractive appearance and ability to imitate wood or stone surfaces, fibrous-cement panels have impressive performance characteristics.
What it is?
Fiber cement panels are a composite material for exterior finishing of buildings. Their basis is made of fiber cement - a mixture of cement (80% of the composition), as well as reinforcing fiber, sand and water (20%).Due to the similar composition and characteristics of the technological process, fiber cement panels have high strength and are characterized by durability. Another name - fiber concrete panels.
Fibrotsement appeared in the late XIX-early XX century and replaced the wooden buildings. Durability, fire resistance of the material led to its instant popularity. However, after a while, it was found that the asbestos in the product adversely affects human health. After this, the search for a safer recipe began, which was crowned with success. Today, fiber cement based siding is an environmentally safe, reliable, and besides, a massively affordable finishing option.
He replaced the plaster, which was previously faced with houses and other buildings. Unlike plastered surfaces, facades lined with fibrous cement are more durable and resistant to atmospheric phenomena, better thermal insulation, ease of installation and a variety of available designs.
For the first time, the material was manufactured in Japan in an industrial way, so it is not surprising that today this country is the leading leader in the production of fiber cement profiles.The quality of the product primarily depends on compliance with the formulation and technological features of production. Raw materials consist of cement, purified cellulose, sand, special components. First of all, dry ingredients are thoroughly mixed, and only then is water added. Next, the raw material is fed to the machines, where the texture of the future product is attached to a special shaft.
After that, the pressing of the raw material under high pressure is carried out to obtain a flat product. The next stage is heat treatment, during which calcium hydrosilicate is formed, the presence of which determines the strength and durability of the panels. Finally, the finished panels are coated with compositions that ensure their moisture resistance and frost resistance. If we are talking about the imitation of a particular surface, then it is at this stage that the coloring and other types of decoration of the panels are carried out.
Specifications
Fiber cement facade panels from different manufacturers may differ slightly in their characteristics, but in general they are the same. One of the brightest characteristics of the panels is fire safety.Cement is non-flammable, so facades cladding ensures complete protection against fire or melting.
Panels are moisture resistant (moisture absorption in the range of 7-20%), and the presence of a special coating protects the material from the appearance of corrosion on its surface. Fiber cement is characterized by frost resistance, it can withstand up to 100 freezing cycles without loss of properties (approximately this number of cycles is calculated for 40-50 years). At the same time it provides high thermal efficiency. The use of plates on the basis of fiber cement can significantly reduce the consumption of insulation, and hence the costs, which is important when facing a private house.
The peculiarities of the composition and the presence of cellulose fiber in it, in addition to high thermal insulation, guarantee good sound insulation. Resistance to impact and mechanical damage allows paneling not only private houses, but also public institutions, to use as a base material.
These properties ensure the durability of the material. - The average service life is 20 years. At the same time, even after several years of operation, the material retains its visual appeal.This is due to the resistance of the panels to the effects of ultraviolet rays, as well as the ability to self-purification.
As for the design, it is diverse. Highlight colored panels, as well as options that imitate stone, metal, brick and wood surfaces. At the same time, the imitation is so high-quality, the texture and shades of the simulated surface are so accurately repeated, so that the “forgery” can only be distinguished from a distance of half a meter.
Unlike plastic or metal panels, fiber-cement counterparts have more weight. On average, it is 10-14 kg / m2, and for thicker and dense panels 15-24 kg / m2 (for comparison, vinyl siding has a weight of 3-5 kg / m2). This causes the complexity of installation in the sense that it is impossible to cope with the installation alone. In addition, the large weight of the panels means an increased load on the bearing elements of the building, and therefore, is only suitable for solid foundations.
Like all panels, these products are mounted on the batten, which reduces the requirements for flatness of the walls.
It is worth noting the wide scope of the material. In addition to finishing the facade, it is used as a windproof and insulating material for the main walls. It is used for operational finishing of frame and pre-fabricated structures for arranging ventilated type facades.
Design
Fiber cement surfaces can mimic a variety of textures. The most popular are products under the tree, under the stone and under the brick. In addition, there are color options. The latter are usually represented by deep pastel shades.
Imitating brick and masonry panels are usually made in red, terracotta, beige, gray and yellow shades.
Particularly noteworthy panel, the outer part of which is covered with stone chips. They not only have an excellent appearance, but also increase the strength and frost resistance of the product. Such panels are a 3-layer cake, the base of which is a fibrous cement base, the back side is represented by a water-repellent coating, and the front side is composed of polyester resins and stone chips.
Dimensions
There is no single standard regulating the size of fiber cement panels.Each manufacturer sets its own standards for the size of the material. In general, their thickness varies between 6-35 mm. If we compare the sizes of Japanese and Russian brands, then the first ones usually have a shorter length, but sometimes turn out to be 2 times wider.
For Japanese plates, the standard dimensions are 455 × 1818, 455 × 3030 and 910 × 3030 mm. For domestic ones - 3600 × 1500, 3000 × 1500, 1200 × 2400 and 1200 × 1500 mm. European models usually have an even wider range of sizes - from 1200 × 770 to 3600 × 1500 mm.
Due to the fact that each manufacturer produces panels in its own size, it is recommended to purchase the entire batch of one brand. This will avoid discrepancies between the plates.
Manufacturers Overview
As already mentioned, among the best fiber cement panels are products of Japanese brands. They are represented by 2 leading companies - Kmew and Nichihaincluded in the Panasonic group. The quality of the original products of these brands is beyond doubt; a wide model line allows you to find the panels of the required design. The disadvantage is only the high cost of production.
Products Nichiha provides high-quality insulation, has a multi-layer coating and almost does not fade.Corner plates and metal corners, as well as other components, greatly simplify the installation process.
Slabs Kmew also consist of several layers. Upper - necessarily paint, as well as ceramic spraying. The task of the latter is to provide high-quality material protection from exposure to UV rays.
Attention deserves the Belgian brand Eternit. Available panels are similar in appearance to painted boards. The manufacturer also resorts to multi-layer coating products. The top layer is a colorful decorative (in the catalogs there are 32 basic shades of the material), the back layer is a waterproof coating that prevents moisture from penetrating into the thickness of the panel.
The trust of buyers is enjoyed by products made in Russia "Rospan"which has been producing fiber cement panels for about 20 years. The material has high strength and weather resistance due to the three-layer coating. The front side is covered first with an acrylic-based facade paint, and then with a transparent silicone compound. Successful is the imitation of stone and wood surface, which is achieved 3-4 mm depth relief pattern. Due to this, it is possible to achieve proximity with the texture of natural stone or wood.
Since the manufacturer focuses on buyers, compatriots, Rospan plates are optimal for use in the Russian climate, including the northern regions.
Another domestic brand, LTM, has made a thorough differentiation of its products, so finding the right panels is not difficult. So, for facing facades in regions with high humidity, panels of the “Aqua” series are provided. If you need to buy panels of increased reliability and durability, models from collections will be a worthy option. "Cemstone", "Cemboard HD", "Natura".
Windproof slabs are characterized by average density and are optimal for cladding high-rise buildings, as well as in coastal regions. Low-density heat-resistant products are used for finishing buildings that are characterized by increased requirements for fire safety. In addition, LTM boards have a wide overall range. For the facades of a large area, larger panels are used. The life of some of them reaches 100 years.
Feature of the company Kraspan (Russia) is the unique elements of the subsystems required to install the panels.The combined use of subsystems and panels allows you to achieve the ideal geometry of the facade, hide defects and irregularities, speed up and simplify the preparatory work. In the manufacturer's collection there are quite bright shades of the panels, although calm pastels prevail.
Another relatively young domestic brand - "Latonite", also receives a lot of positive customer reviews.
In their lineup you can find the following types of panels:
- painted pressed plates (suitable for interior and exterior use);
- unpainted extruded products (intended only for external cladding, require further staining);
- panels not pressed unpainted (used for interior design, suggest the subsequent application of paint and varnish compositions);
- fiber cement siding (common fiber cement based siding profiles).
In the collections you can find many panels of bright color, there are also pastel shades. In addition, the buyer can order the coloring of suitable panels in the selected shade according to the RAL-catalog.
In the next video you will see an overview of fiber cement facade plates of the A-TRADING company.
How to choose?
When choosing panels, give preference to those that are supplied with complementary elements and fittings. Such sets will cost more, but there is no doubt that the components and accessories will be compatible. It is important to accurately calculate the required amount of facing material and not to forget about a small margin for scrap and trimming. As a rule, for buildings of simple construction, it is enough to add 7-10% to the reserve, for buildings of complex configuration - 15%.
The weight of fiber cement panels is quite noticeable, so you need a reliable and high-quality crate. Many manufacturers produce profiles for the assembly of crates, which are designed for panels of specific panels of the same brand.
Many users consider it optimal when a set of panels, in addition to fiber-cement plates, includes additional elements and accessories, profiles for creating a batten, acrylic paint for processing cuts, as well as assembly instructions. Suspended fiber cement material necessarily includes decorative panels and profiles of metal.
It has already been said that fiber cement panels are sometimes called fiber concrete. Such ambiguity of the name should not confuse the buyer, it is one and the same material. Just some manufacturers prefer to call the plates fiber cement.
Japanese panels often have a glass ceramic layer that provides improved protection against weather conditions. In this regard, products from Japan have a higher cost. In addition, shipping costs are included in the price of products. Do not forget about this when buying - a quality product can not be cheap.
On average, the cost of the material ranges from 500 to 2000 rubles per m2. The cost depends on the size and thickness of the panels, features of the decoration of the front side, performance indicators, brand.
Recommendations for working with the material
The technology of installation of fiber cement panels is simple, but it is necessary to follow a number of specific recommendations. First of all, you should decide on the type of installation: directly to the walls on the screws or on the batten. In any case, you will need staples, through which screws are screwed. Klyymery serve to improve the fixation of the panels, as well as to hide the horizontal seams between them.
In most cases, lathing is used, thanks to which between the wall and the panel it is possible to preserve the air gap, use insulators and not strive for perfect alignment of the walls. For crates used wooden beams or metal panels. The latter do not require special training, unlike the wooden counterpart.
A frame installation is quite easy, in which metal frames are fixed on the crate. Panels are screwed into their grooves.
Sometimes the panels are mounted without highlighting the basement zone from the blind area to the eaves. The framework for all panels is shared. If it is necessary to allocate the basement or to fill the insulation between it and the plates, the frame in this part is somewhat compared to the crate of the rest of the facade.
As a heater, claydite of a different fraction is usually used, which is characterized not only by high thermal insulation performance, but also helps to protect the structure from rodents.
Installing fiber cement siding panels is no different from mounting siding. The process significantly simplifies the presence of special grooves and locking mechanisms.
If it is necessary to cut the panels, it is necessary to process the cuts with acrylic paint. Usually it is included and sold with the material. Such processing of the cut will ensure the uniformity of shades on the panel and sections, as well as protect the material from moisture penetration and further destruction.
The joints between the panels should be treated with silicone sealant. If it is necessary to paint the panels, make sure that the surface is flat and clean. If necessary, grind the coating, and then remove dust and dirt by air blowing over the surface.
Beautiful examples in the exterior
Fiber cement panels successfully imitate different types of wood.
They successfully imitate metal siding, differing, with higher performance.
Finally, the material in question can “transform” into colored panels that resemble vinyl or acrylic siding in unusual colors.
To create exquisite respectable exteriors, it is recommended to use stone or brick masonry panels.
It looks interesting combination of panels of different textures.Wood and stone, stone and brick, brick and metal elements are harmoniously combined.
When choosing the texture and shade of the facade, it is important that they look harmoniously in the exterior, combined with the color scheme of the entrance group, household buildings. The easiest way to select a house or other building among others is to choose bright panels for its decoration. At the same time, the dimensions of the facade will increase visually.
If there are interesting architectural elements in the house, it is recommended to highlight them in color. Organically look buildings, decorated with panels of light shades with darker turrets, columns, protrusions and other elements. Contrast can be achieved through the use of various textures, for example, the main part of the facade is lined with wood-like material, architectural elements - under stone.
If the house is surrounded by a garden or a park, designers are advised to choose light pastel shades for decoration. For buildings in the city, you can pick up bright colors or expensive textures.