How to dilute epoxy glue: the correct proportions
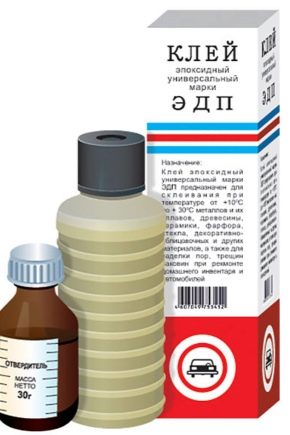
Very often, both in everyday life and in production, means are required for bonding materials. Epoxy glue is one of the most used types of adhesives and has many advantages. But like any tool, epoxy adhesive has its own characteristics that affect the final result.
Special features
Before proceeding to the bonding of surfaces, it is necessary to understand the composition of the adhesive, the principles of its action and scope.
What is epoxy glue made of? The answer to this question lies in the very name of the glue. It is based on epoxy resin, which is a type of synthetic resin and has universal consumer properties.
For curing the resin requires a certain temperature. For epoxy, it ranges from -10 to +200 degrees. The choice of temperature depends on the type of composition. Depending on what temperature the reaction will take place, epoxy resins are divided into cold and hot types of curing. The cold form is used for materials that are not subjected to heat treatment, and hot types are needed for materials that can withstand not only high temperature, but also the effects of active chemical substances.
Cold curing is most often used for bonding materials at home.and also used in small industries. For large industrial enterprises, hot curing is the most appropriate. Aircraft, mechanical engineering, electrical engineering, electronics, shipbuilding and other industrial areas use epoxy resins as part of glue.
In addition to the epoxy resin, the adhesive contains a hardener, without which the polymerization process is impossible. It is the hardener that reacts with epoxy resin to help it harden and not melt.
In the sale of resin and hardener are in different bottles, for bonding these components will have to be diluted in the required proportions. Both components belong to polymers with a small molecular weight, when interacting simple molecules combine, resulting in a large polymer molecule (with full solidification).
To speed up the polymerization process, you can increase the temperature and increase the amount of hardener, and to slow down the reaction, do exactly the opposite, lower the temperature and reduce the amount of hardener.
The universal composition of epoxy glue has a high degree of adhesion., they can glue together almost any material: metal, rubber, glass, plastic, wood, the main thing is to combine resin and hardener in the right proportion. After complete curing, the surface treated with this composition can undergo any treatment: grinding, sawing, drilling and other types of work can be carried out without deforming the material.
How to breed?
Dilution of glue requires maximum care, so it is better to prepare in advance all the necessary tools and means of protection.
Rubber gloves and a mask will be required to protect the skin and respiratory tract, because both components are extremely toxic substances. Capacities for dilution of components and sticks for their mixing are necessary. In addition, the room in which the work will take place must be well ventilated.
Depending on the composition of the epoxy, it can form compounds of different stiffness. For a soft elastic coupling, one type of compound is produced, and for a firm one, completely different. Therefore, it is necessary to acquire components and prepare the adhesive composition, strictly observing the proportionality specified by the manufacturer.
Usually instructions are attached to bottles with pitch and a hardener., which always indicates how to mix the ingredients correctly, while respecting the proportionality of the dilution. As a rule, for the preparation of the adhesive composition is required to dilute the components 10: 1 - 10 parts of the resin accounts for 1 part of the hardener.
But manufacturers today produce different compositions, which are not always required to be diluted in this way, sometimes in order to prepare the adhesive composition, it is required to mix the resin and hardener in a different proportion.
The proportionality of the dilution depends on the specific manufacturer.In one case, the ratio may be 10: 4, in the other - 10: 6, and in the third, 4 parts of the hardener must be diluted in 6 parts of the resin to achieve the desired consistency. The proportionality of the dilution depends not only on the specific manufacturer, but also on the release date of the resin and hardener, storage conditions, ambient temperature, and, of course, on the quality of both products.
Previously, in order not to be mistaken with the number of added components, manufacturers produced bottles with marks, but today there are no divisions on the bottles, therefore, the ingredients can be mixed using different improvised means.
To mark a small amount, you can use the old stem from under the handle. Before use, it is thoroughly washed and marked on the surface at regular intervals.
Measure the amount of the component, you can use and more convenient tool - a syringe. There are already marks on it, you do not need to draw them yourself, and they are much more accurate than they were personally made on the rod. To pour the hardener into the syringe, you just need to remove the needle and pump it through the piston,and the resin will have to be placed in it in a slightly different way, because it will not work to pull it through the spout - it has a consistency too viscous. In the syringe, it is necessary to remove the needle, remove the piston and plug the nose, and only then pour the resin through the top.
In order to properly mix the epoxy, you need to start each component to prepare for breeding. A measured amount of viscous transparent resin is added to the container and mixed thoroughly. Sometimes epoxy is mixed very hard, so to facilitate this process it can be heated in a water bath, 50-60 degrees is enough. But it is worth remembering that increasing the temperature not only facilitates mixing, but also speeds up the polymerization process - it is enough just to increase the temperature of the mixture by 10? C, and the reaction will accelerate by 2-3 times.
After preparation, the components must be combined and stirred in a clean container, but this should not be done very vigorously, otherwise the appearance of bubbles does not escape. Their presence in the glue can spoil the appearance of the poured objects, if the composition is used as a fill.
For simple bonding of surfaces, the number of bubbles does not matter. If dyes are added to the composition, it is better to use them in a dry form, since moisture, even in the smallest amount, adversely affects the adhesive composition.
The prepared composition during the first minutes is distinguished by a liquid consistency, but after 10–15 minutes it begins to thicken quickly, and after 30 minutes it solidifies. To extend the working time with the composition, you can use a tool such as acetone - it will increase the glue lifetime to 1 hour. To do this, it is necessary to dissolve only 1 part of this substance in the composition with a proportion of 10: 1: 1.
How to use?
It is not enough to prepare the composition, you need to use them skillfully. Glue can be used both as a connector of surfaces, and as a fill in prepared forms.
For durable bonding materials, there are general rules for preparing:
- mechanical cleaning of the surface of materials from contamination;
- degreasing the prepared glueing sites from oil traces; a solvent, acetone or detergent will be suitable for this;
- Glossy surfaces are treated with sandpaper or a grinding wheel.
For simple bonding, the composition is applied to one of the sides, after which both surfaces are pressed tightly against each other. As clamps, you can use a strong rope, vise, clamps or cargo. Any residual glue is removed with a dry cloth or tissue. In a fixed position, the glued materials must be kept for at least 24 hours while the primary polymerization process is in progress, after which the auxiliary fasteners are removed and the product subjected to gluing is left to dry completely for 7 days.
When using special molds, they are prepared differently. The bottom and sides are treated with fats. After lubrication, the finished composition is poured into the mold and kept there until it is completely cured. To increase the rate of polymerization after a 3-hour hold of the mold at room temperature, it is sent for heating to the oven. If the form is not subjected to heat, the process of complete curing can take up to 7 days.
Tips
When preparing the composition, as well as when it is applied to the surface or when the mold is poured with this glue, there are universal tips that help to achieve better gluing.
In the preparation of the composition is better to use dishes and auxiliary tools, unnecessary for further use. It is almost impossible to clean them of such a composition, therefore all used containers and tools for mixing will be emitted.
Filling in the form must be carried out in stages, especially if you plan to make the layer thickness greater than 2 mm. After polymerization of the first coating, the next portion is poured only after the layer is cured, but with a sticky surface.
For larger volumes it is better to buy special formulations.not subject to overheating. When mixing a large amount of conventional glue, there is a risk that the composition will ignite. Therefore, for your own safety, it is necessary to calculate in advance the required volume of the mixture and buy glue, calculated specifically for this volume.
How to dilute epoxy glue, see the next video.