Types and sizes of double brick
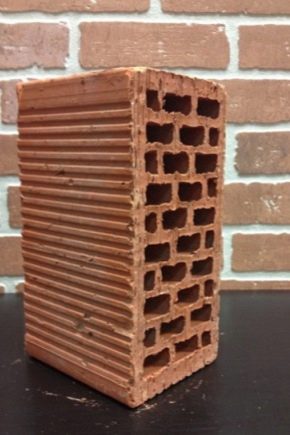
During the construction of buildings, many craftsmen face the choice of building material, which should have not only aesthetics, but also have high performance. All these parameters are answered by a double brick, therefore recently it is in great demand. In addition to reliability and durability, double blocks also allow you to speed up the process of construction, and 2 times less cement mortar is used for their installation.
Special features
Double brick is a universal building material, inside which there are voids. His indicator of strength and endurance is determined by a special marking in the form of numbers, standing after the letter "M".For example, for the construction of multi-storey buildings, it is recommended to choose the double blocks M-150. If construction of walls alone is planned, then an M-100 brick will be suitable.
For the manufacture of double-brick, only ecological components are used, usually this is top-quality clay, water and natural fillers. Material production is carried out by both foreign and domestic brands. Depending on the manufacturing technology, one can consider a slotted and porous block. In this case, the first type differs from the second one by the presence of gaps and openings of different sizes inside. Due to the internal voids, the weight of the product is reduced.
To date, the manufacture of double bricks improved, and allows you to produce blocks of different size range that exceed the established standards. Depending on the characteristics of production, the material may differ not only in appearance, structure, but also in performance. Double brick is produced in the following ways.
- Plastic. Initially, the clay mass is prepared with a humidity of 18-30%, and a preform is formed from it.Then the raw material is sent to the molds, is pressed and burned in the chamber at a high temperature. The result is a durable double ceramite, which is ideal for building houses and utility blocks in areas with high levels of humidity.
- Semi-dry. In this case, the technology provides for firing the workpiece with a moisture content of not more than 10%. According to GOST standards, such blocks should contain two ceramites, and brick sizes should be 25 × 12 × 14 mm.
Thanks to modern equipment and various additives, double bricks can be produced not only in traditional brown or red, but also in other shades. This simplifies the choice of material during construction, as it is ideal for any design project. Double brick is used in almost all construction sites, they lay out both the external, internal walls and the foundation. The advantages of such units include:
- high heat preservation;
- durability;
- air permeability;
- reasonable price;
- quick styling.
As for the shortcomings, this material of some species has a large mass, therefore, in hard-to-reach areas, its layout can be complicated.
Species
The popularity and huge demand for a double brick is explained by its high operational performance. It may differ in texture, size, number of slots and voids. Depending on the raw materials used for manufacturing, there are two types of blocks.
Silicate
Their main feature is that the production is carried out from a mixture consisting of 90% sand and 10% water. In addition, the product also contains additives that increase its quality. This is an absolutely eco-friendly material that looks similar to a natural stone. The process of manufacturing a double silicate brick occurs by pressing a wet mix of lime and sand, after which various pigments are added to it, and sent for steam treatment. It can be hollow, slotted, or porous. By strength, silicate blocks are divided into marks from 75 to 300.
These blocks are most often used for laying out internal and external partitions. Silicate brick cannot be used for the construction of socles and foundations of buildings, since the product is not resistant to moisture, and in the absence of a waterproofing layer may be subject to destruction. It is not recommended to make a double silicate brick and laying pipes, furnaces.It will not withstand prolonged exposure to high temperatures.
As for the advantages, then this product has excellent sound insulation and has the correct geometric shape. Despite the heavy weight of such bricks, their laying is quick and easy. By their density, silicate products exceed ceramic by 1.5 times, so they provide durable and high-quality masonry. In addition, silicate double blocks are 30% cheaper than other types.
Depending on the design features of this material is divided into facial, slag and ash. Each of these subspecies is intended solely for the construction of specific objects.
Ceramic
Represent a modern building material, which is used in almost all types of construction work. Its feature is considered to be large sizes, which are usually 250 × 120 × 138 mm. Thanks to such non-standard dimensions, construction is accelerated, and the consumption of concrete fill is significantly reduced. In addition, double ceramic brick is not inferior in strength to conventional blocks, so it can be used in the construction of bearing and self-supporting structures in buildings with a height of not more than 18 m.The product is characterized by high thermal insulation, the buildings laid out of it are always warm, and they always maintain an optimal microclimate.
The main advantage of a double ceramic brick is its affordable cost, while many manufacturers often make good discounts when purchasing blocks for building a large facility. These blocks, in addition to high quality, also have an aesthetic look. Typically, brick is red in color, but depending on the additives it may also acquire other shades. The product is environmentally safe, and even with prolonged use and exposure to the external environment does not emit harmful substances.
These blocks are transported on pallets, where usually up to 256 pieces are placed. As for marking, it can be different, most often for the construction of objects choose the brick M-150 and M-75. In addition, double ceramic blocks are divided into full-bodied and hollow, not only their price, but also their heat capacity depends on this parameter. Hollow brick can not be used for the construction of load-bearing walls, in this case only full-bodied is allowed.Despite the fact that the former has a low weight and significantly reduces the overall load on the foundation, its inherent gaps affect the thermal conductivity.
In addition, the double brick is divided into the following types.
- Private. These blocks are ideally suited for laying stoves, fireplaces and arranging the foundation. The only thing is that when the facial display requires additional finishing.
- Facial. It is produced in clinker and hyperpressed versions. It can be either solid or hollow brick. Unlike ordinary blocks, facial ones are produced in a figured, trapezoidal, rounded and twisted form. As for the color, it is dark brown, gray, red, yellow and brown.
Dimensions
One of the features of a double brick is considered its dimensions, which are almost 2 times larger than the dimensions of single and one-and-a-half blocks. It is worth noting that the weight of the product is small, therefore reducing the overall load on the base of the building. This is explained by the presence of voids inside the blocks, which can take up to 33% of the product space. According to construction standards according to GOST 7484-78 and GOST 530-95, double bricks can be produced in the size of 250x120x138 mm, while foreign manufacturers can manufacture products of other sizes. In addition, the dimensions of bricks depend on the raw materials from which it is released.
- Double ceramic block. Its dimensions are 250 × 120 × 140 mm, this material is designated as 2.1 NF marking. Since brick sizes are 2 times larger than the parameters of standard blocks, this indicator significantly influences the height of the calculation.
- Double silicate block. It is also produced with a size of 250 × 120 × 140 mm, with such indicators for 1 m3 of masonry up to 242 pieces of blocks are required. Despite the specified dimensions, such a product has a decent weight of up to 5.4 kg, since in the manufacture of blocks, auxiliary components are added to the composition that enhance the frost resistance characteristics.
Double bricks are manufactured strictly according to the technology and established standards, but since the block blanks in the production process are fired in kilns and additional processing, their sizes can vary in parameters up to 8%. To prevent such changes in size, manufacturers at the stage of forming bricks increase their geometric data. In the end, after the release of typical products. Notwithstanding this, GOST allowed a deviation from standard dimensions in length by 4 mm, and in width by no more than 3 mm.
How to calculate the quantity?
The construction of new facilities is considered responsible work, so it must be started not only with the design, but also with the calculation of the material. First of all, they make counting the number of bricks in one cube. For this it is also important to take into account the thickness of the seams and the width of the laying. Usually, up to 242 units of double brick per 1 m3, if you subtract the seams, then the figure will be 200 pieces, thus, for each calculation of 1 m2 without taking into account the seams 60 blocks are required, and taking into account - 52. These calculations are suitable if the constructions are planned to be laid out in one row, no more than 250 mm thick.
For structures with a thickness of 120 mm, 30 units are needed without consideration, and 26 with regard to seams. When building walls with a thickness of 380 mm, the consumption will be, respectively, 90 and 78 pieces, and for a thickness of 510 mm - 120 and 104 units. In order to get a more accurate figure in the calculations, it is recommended to lay out one or several test rows without a solution for illustrative example, and only then calculate everything.
In addition, brick consumption depends on the type of construction work and the number of voids inside the blocks, since hollowness can take up to 50% of the volume. Therefore, if you plan to build without additional wall insulation, it is recommended to choose a brick with a large number of slots,as it will provide the minimum load on the foundation, it will make the building warm, and a smaller number of blocks will be needed for laying.
Despite the fact that double bricks are produced in standard sizes, their batches may differ by a small percentage of error. Therefore, for the construction of large buildings it is recommended to place an order at once of the entire number of bricks. This will relieve not only of the problems with calculations, but will guarantee the same shade of products.
How to calculate the number of bricks for masonry, see the following video.