The subtleties of the process of finishing slopes sandwich panels
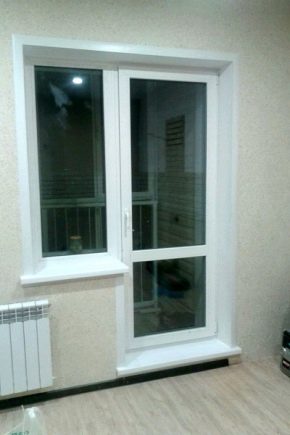
The freezing of the structure and the formation of condensate can ruin the appearance of even the highest quality and expensive window system. There are many methods for finishing window slopes. Most of them can only be performed by professionals, but there is the simplest variation to solve this problem. This use of sandwich panels for slopes, installation of which can be done by hand.
Special features
In contrast to old wooden frames, modern plastic windows are equipped with special equipment for ventilation.For this purpose, the upper part of the window frame is folded back, forming a narrow opening for fresh air. As a result, air turbulence with sharp changes in temperature conditions occurs.
In order for the entire window system to last a long time, it is necessary to take care of the design of the window slope.
Often, drywall is used for this purpose, but such building materials can freeze through during the winter period, and caring for it requires great effort.
If the room is built of brick or reinforced concrete blocks, only sandwich panels can be used for maximum warming of slopes.
Many experts recommend using plastic with a cellular structure, but such products have insufficient strength and density, and the installation of the structure is laborious.
The advantages of using sandwich panels are as follows:
- additional noise and heat insulation is performed. Additional insulation is carried out by means of polyurethane foam for a better connection of the material with the slope;
- does not require constant care and maintenance. Any kinds of pollution can be easily washed off with a cleaning solution without damaging the structure;
- high vapor permeability. Unlike plasterboard material sandwich panels do not get wet and do not crack under the influence of moisture;
- low weight of the structure (weight of 1 m² with a thickness of 24 mm is 3.9 kg);
- high resistance to mechanical damage;
- resistance to ultraviolet radiation;
- stylish appearance of a design;
- resistance to the formation of mold and fungus;
- acceptable cost of the product;
- do not require additional clearance. The surface of the panels has a structure similar to the surface of plastic windows;
- environmentally friendly material. Does not emit harmful substances, thus does not harm living organisms during the period of operation.
Despite the fact that multi-layered panels have a lot of advantages, some consumers have negative reviews about this building material, such as:
- under the influence of high temperatures, the product turns yellow and deforms;
- improper installation of the material may lead to the formation of gaps and cracks;
- finishing slopes using sandwich panels can not be performed if the distance between the loop and the wall is small.Otherwise, the construction will walk around the perimeter;
- only low quality materials have such disadvantages.
Specifications
Specifications of the sandwich panels for creating window slopes are as follows:
- sound and sound insulation index is not less than 21 dB;
- density - 30–35 kg / m³;
- compressive strength - 0.25 MPa;
- thermal conductivity of the product - 0,029 W / (m • K);
- product flammability class - G1;
- the operational life of the material is about 50 years;
- temperature range for operation - from -50 to +60 degrees;
- heat conductivity in a dry room - not less than 0.041 W / (m² • K).
Device
Sandwich panels are sheets made of extruded polystyrene foam. Their thickness is 9 mm. Such sheets can be trimmed on one or both sides of PVC sheets, the thickness of which can be 1 or 1.5 mm. The dimensions of the sandwich panels for window slopes are 300x150 centimeters.
The material consists of elements such as:
- Profile C-and J-shaped. The C-shaped profile is mounted from the side of the room. The special element is intended for fixing the inner boundary of the slope;
- wooden beam, which is suggestive;
- polystyrene insulation material that fills all cavities. Thanks to such a product, blocking the cold intake from the street;
- the top panel, which is the decorative finish of the building.
The following materials can be used as insulation materials:
- polyurethane foam;
- extruded polystyrene;
- loose plastic.
The outer layer of a multilayer product can be made of several building materials.
- Hard PVC sheet. For the manufacture of multi-layered panels used sheet material in white. Thickness can vary from 0.8 to 2 mm. Special coverage sheet can be matte or glossy. Product density is 1.4 g / m³.
- PVC sheet foamed. The internal part of the structure has a porous structure. PVC foam sheets have a small density indicator (0.6 g / m3) and a good thermal insulation value;
- Laminate. Such a material is made by impregnating a multilayer material with resins, consisting of decorative and kraft paper, followed by pressing.
The top panels of the design can be of various color shades, which allows you to choose a panel for any window.
Sandwich panels can be produced by ready-made systems, in this case there is no need to carry out the preparatory work on the assembly of building materials. The finished systems are fixed to the facing building material with an adhesive solution. The second variation of the system - such products are assembled by means of self-tapping screws before installation.
Multi-layer panels are one-sided and two-sided production.
- One-sided manufacturing is when one side is rough and the other is front. The front side is thicker than the rough.
- Bilateral material is when all sides of the product are facing. Many believe that sandwich panels are designed only for plastic windows, but they can also be used for wooden ones.
There are metal panels, which are mainly intended for the construction of hangars, sheds. Installation of such panels for PVC windows has a number of difficulties. The opening must be sheathed with a profile or board, after which you can install metal panels.
The installation of slopes from sandwich panels is important for such reasons as:
- protection of seams against destruction, therefore lining of plastic windows should be carried out both indoors and outside;
- as an obstacle to the penetration of moisture from the street and the appearance of condensate;
- improvement of thermal insulation indoors. Cold air will not penetrate inside the room, and thermal energy will not go outside.
Design solutions
The construction market offers a wide range of decoration panels for slopes. You can choose the design of any shade. The most popular is the white color, but connoisseurs of an elegant image in the room can pick up non-standard variations of colors.
Now yellow shade is very popular. You can set the panel to the color of the glass or pick up a harmonious shade. Demand is the design of slopes in a natural style. The slopes trimmed with a material imitating wood look harmoniously. Panels for window slopes can be used for any stylistic decision.
Dimensions
The parameters of the sandwich panels depend on the equipment used by the manufacturer.However, there are standardized sizes. The maximum length of the panels can be from 12 to 16 meters. The large size of the product may cause the product to fracture under its own weight during the installation process, and it will also be difficult to transport the material. The width is 100, 115 and 119–120 centimeters, and the thickness can vary from 5 cm to 35 centimeters.
In some cases, the panels are made according to the preferences of the customer. There are sandwich panels, the technical characteristics of which allow them to be used for finishing the slopes of windows and doors. The parameters of such panels are 3000 in length, 1150, 1300 or 1500 mm wide, and 10 mm in thickness. In rare cases, the thickness of the products can be 24, 32, 40 mm.
Installation
The process of mounting slopes sandwich panels consists of several stages. To finish the slopes, you will need tools and equipment such as:
- roulette, construction level, pencil, bolkarka or assembly knife;
- U-shaped plastic profile, profile profile, liquid nails and construction pistol;
- screwdriver and screws;
- white sealant, primer mix for concreted substrates, brush and antifungal special agent;
- plaster, trowel, sandpaper, medium grain, drill.
Preparatory stage
Sandwich panels are practical building materials that are simple in installation. Panels are double-layered and three-layered. The last variation of the material is covered with PVC on both sides. These panels are suitable for installation on a wooden frame, because they have increased cruelty, it is pointless to mount them on a wall surface or on liquid nails, because PVC material has a low rate of adhesion with such building material.
Installation of slopes of this type is performed by three methods: on liquid nails, foam, or on a frame of wooden bars.
Consider the first variation of the installation, that is, on the initial profile and liquid nails, which deals with minimal space. In this case, the thickness of the double-layer sandwich is 10 mm. At the preparatory stage, the cleaning of the slopes is performed, everything that can lead to the peeling of the product from the base is removed. Irregularities and bumps are eliminated.
If after installation of windows there are excess construction foam, they must be removed.And also all areas that are not involved in the installation, you need to cover with plastic wrap, which would prevent the destruction of the window sill and window.
After preparing the plaster mixture for rough work. This mixture closes up all the cracks and cracks, the surface should be perfectly flat. This can be verified by building level. If the surface of the slopes was originally in perfect condition, then the process with plaster can not be performed.
After the plaster mixture has completely dried, the slopes are treated with a primer mixture designed for porous surfaces. This is necessary in order for the glue to securely fasten the sandwich panel. After the primer mixture has dried, the base is treated with an antifungal special agent, after the product dries, you can proceed to the lining of the window slopes.
Installation of sandwich panels
First you need to take measurements of each window slope, as well as cut sandwich panels under the parameters of slopes. Cutting is done cutting. Cutting panels is more efficient with a mounting knife. To do this, fit the panel on the floor, and mark up with a pencil and tape measure.Now the devil is cut with a knife blade, after which this procedure is repeated several times, trying to get into the first cut. When the material is cut, the edges of the cuts need to be leveled with sandpaper.
The following procedure is the installation of side slopes. By means of self-tapping screws fastening of a starting profile is carried out. The distance between the screws should be 15 centimeters. Installation of the panel can be done without installing the original profile. In this case, the panels are mounted close to the window, turning 1 cm deep behind it. Fixing the slope is done by zaping. This is a more complicated installation option, but the final result of the design looks more aesthetic.
Then a zigzag strip of liquid nails in the middle and straight stripes along the material perimeter are applied on the panel. The panel is inserted with one edge into the starting profile and pressed against the slope. In the same way, the top and second side panels are installed. For decorative decoration of the window opening along the perimeter, a profile profile is glued. In order for the window to have a neat appearance, the area of the joints in the corners must be cut at 45 degrees.
When installing sandwich panels, you should try to install component parts in such a way that there is a minimum gap between them.
To mask the joints, you can use a white sealant or liquid plastic. At this stage, the finishing of the slopes with multilayered panels is completed, but it is necessary to wait 1–2 days for the construction to completely dry. Correctly installed slopes are functional and do not require special care, they are designed for a long operational period. Building materials are not modified by exposure to ultraviolet rays.
Foam installation
For this finishing option, you need to purchase a multi-layered panel having two stiffeners. This process includes the following steps:
- measurements are performed. It is necessary to obtain accurate indicators so that in the future there is no error when cutting the material;
- installation of the starting profile;
- prepared measurements are transferred to the facing building materials;
- the panel is trimmed with a sharp object;
- mount the top bar. It must be inserted into the groove of the starting profile;
- the gap between the panel and the wall is sealed with mounting foam.Apply the foam should be carefully, because during the drying period the foam will increase by 2 times. It is recommended to choose a professional version of the mounting foam, which is applied with a thin layer;
- immediately install a plastic special element that is made using masking tape;
- next, the lining of the vertical sections with sandwich panels is performed;
- give time for complete drying of the foam, the excess material is cut off.
Mounting on wooden slats
This version of the editing work includes the following actions:
- taking measurements and transferring them to the panel. Details are cut to the required dimensions;
- on the edge of the window frame on the outside are mounted wooden slats. As a result, a complete contour should form. The correctness of the installation is determined by the construction level;
- the profile is fixed to a plastic frame;
- a small gap is formed, which can be filled with mineral wool or polyurethane foam;
- Multilayer panels are inserted into the profile grooves, but they are not glued, but nailed with a construction stapler. Staple punch the outer side of the PVC panel, so this variation is suitable for a three-layer product;
- if you do not use the starting profile, then all the elements need to be glued. In this case, the inner corner is treated with a sealant to hide the resulting defects.
Tips and tricks
The design of window slopes with sandwich panels has such technical features that need to be considered, such as:
- if you live in hot climatic conditions, you should use panels with renolitic special coating, this film can withstand higher degrees;
- during the mounting of the structure it is worth paying attention to the coefficient of linear expansion coefficient;
- for cutting material instead of an assembly knife, you can use a circular saw with a small tooth pitch, which will prevent cracking or delamination of the product;
- It is not recommended to cut the panel at low temperatures (less than +5 degrees). Low temperatures lead to material brittleness;
- when installing the panels, the starting profile should be applied as recommended by the manufacturer;
- When using the installation of panels by means of wooden slats, it must be made of dry wood. Before installation, the rail must be treated with a special impregnation.If this is not done, the building material may be subjected to deformation under the influence of moisture;
- Before acquiring the trowel mix for joints, you need to check that its shade fully matches the color of the plastic elements. Otherwise, in the future, the joints will stand out against the general background of the structure.
On how to mount slopes from sandwich panels, see the following video.